Back to blog
Optimize supply planning processes with Lumi AI
.png)
What is Supply Planning?
Supply planning ensures that businesses have the right products available at the right time to meet customer demand. It’s an important process that balances inventory levels, production schedules, and supplier relationships to achieve operational goals like on-time delivery and cost efficiency. Effective supply planning aligns resources with forecasted demand, optimizing the supply chain to stay competitive in dynamic markets.
In today’s fast-paced business environment, supply planning is more than just an operational task - it’s a strategic advantage. Companies that excel in supply planning can adapt to demand fluctuations, mitigate risks, and reduce costs, giving them an edge over competitors. By integrating advanced tools and technologies, businesses can enhance decision-making and ensure resilience in their supply chains.
Supply planning works hand-in-hand with demand planning to create a seamless supply chain. While demand planning forecasts how much of a product will be needed, supply planning focuses on how to meet that demand using available resources. These complementary processes ensure businesses can maintain balance—meeting customer needs without overstocking or understocking. By leveraging internal data and aligning it with demand forecasts, supply planning drives efficiency and agility across the supply chain.
Key Differences in Objectives: Supply Planning vs. Demand Planning
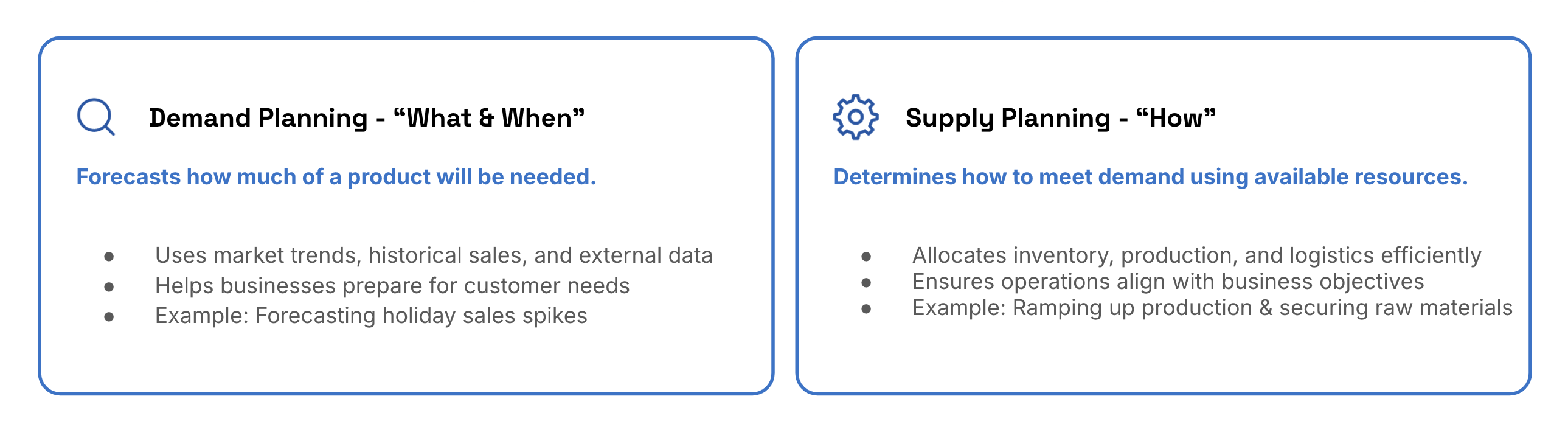
When comparing supply planning and demand planning, the differences lie in their focus and end goals.
- Demand Planning answers “What & When”. Demand planning revolves around anticipating future needs by analyzing market trends, historical sales data, and external factors. Its purpose is to provide accurate insights into what customers are likely to require, allowing businesses to prepare appropriately. Think of it as the "what and when" component of supply chain management.
- Supply Planning answers “How”. On the other hand, supply planning is all about execution. It takes the insights from demand planning and turns them into actionable strategies. This involves determining "how" to fulfill the anticipated demand while optimizing available resources like production capacity, inventory, and supplier capabilities. Supply planning doesn’t just react to forecasts—it aims to align operations with broader business objectives, whether that’s minimizing costs, ensuring rapid delivery, or balancing both.
Consider a real-world example: During the holiday season, demand planning might predict a significant spike in sales for popular items. Supply planning takes this forecast and determines how to make it a reality—by ramping up production, securing additional raw materials, optimizing warehouse space, and coordinating logistics to handle the increased volume. Without the "how" of supply planning, even the most accurate demand predictions could fail to translate into business success.
By working together, demand and supply planning create a balance that enables organizations to achieve both financial and service goals. Demand planning identifies the need, and supply planning ensures the resources and strategies are in place to fulfill it, creating a robust and resilient supply chain.
Current State of Supply Planning
Today, many organizations still rely heavily on manual processes to manage supply planning. Below is an overview of the current process:
- Data Collection: Compilation of inventory levels, demand forecasts, lead times, and supplier performance metrics from multiple systems.
- Data Reconciliation: Resolution of mismatched information to establish a consistent and reliable baseline.
- Inventory Analysis: Evaluation of stock levels, safety stock, and reorder points to identify risks like stockouts or overstocking.
- Supply-Demand Alignment: Comparison of supply availability with projected demand while accounting for production and supplier constraints.
- Capacity Planning: Assessment of labor, equipment, and material availability to meet projected demand.
- Production Scheduling: Development of schedules to allocate resources efficiently based on material availability and delivery timelines.
- Procurement Coordination: Collaboration with procurement teams to confirm lead times, manage order quantities, and optimize supplier arrangements.
- Optimization Decisions: Evaluation of trade-offs between cost, efficiency, and responsiveness to finalize plans and mitigate risks.
These manual workflows consume valuable time, increase the risk of errors, and limit the ability to respond to unexpected changes in demand or supply chain disruptions. Without real-time insights, planners may miss opportunities or face costly delays.
In the next section, we’ll explore how Lumi AI streamlines these manual processes and empowers supply planners with advanced tools and insights to optimize their workflows and improve overall efficiency.
Supply Planning using Lumi AI
Lumi AI is an enterprise data & analytics platform that allows supply planners to explore data, create custom reports, and derive actionable insights using plain language prompts—no python or sql needed—unlocking hidden value, boosting productivity, and reducing reliance on overburdened data teams.
Supply planners at mid-to-large CPG and F500 retail clients using Lumi uncovered multi-million dollar opportunities hidden in inventory, sales, and procurement datasets, driving faster, more informed decisions.
Supply Planning Use Cases:
- Uncover Procurement Savings: Identify opportunities to negotiate better terms or optimize order quantities for cost efficiency.
- Optimize Inventory Levels: Flag excessive stock, nearing-expiration items, or inefficiencies to reduce waste and improve stock management.
- Analyze Demand Trends: Examine raw material and finished goods consumption patterns to align supply with demand effectively.
- Generate Exception Reports: Create actionable lists for underperforming items, stores, or regions to address anomalies and improve performance.
- Uncover Root Cause: Identify supply chain disruptions by analyzing outliers in lead times, supplier performance, and demand fluctuations, enabling proactive issue resolution.
- Share Insights with Team: Provide team members with key findings to align strategies and enable collaborative action.
Case Study
Using Lumi to Identify Excess Inventory and Over-purchasing
Objective: Determine potential procurement inefficiencies. Focus on uncovering over-purchasing, or supply chain imbalances to inform corrective actions and optimize future procurement strategies.
Prompt: Which items have the highest months of supply? Assume the date is Sept 1st 2023.
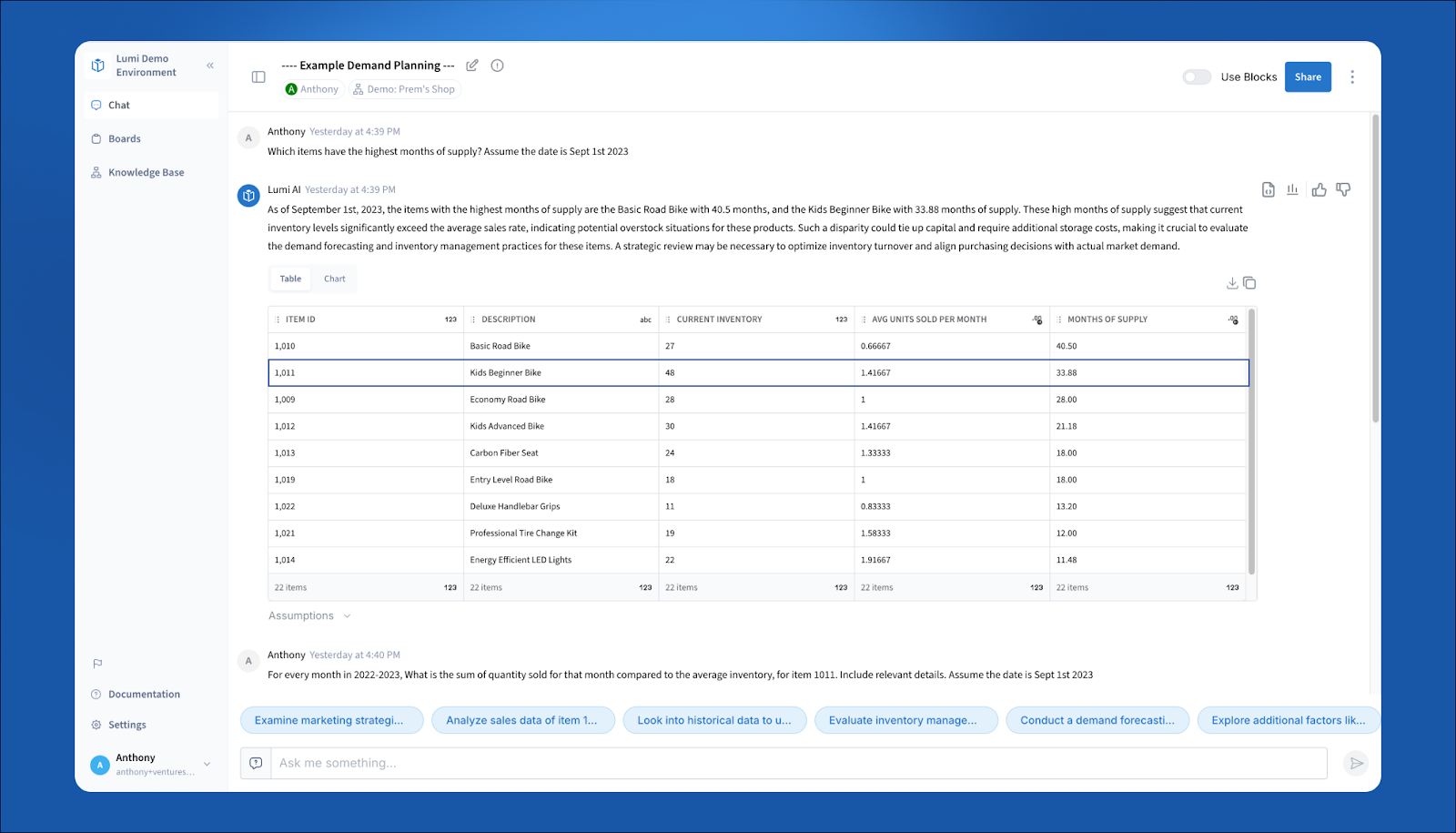
Outcome: Generated a targeted list of items with potential inventory management improvement opportunities. The analysis revealed that the item Kids Beginner Bike has 33.88 months of supply, indicating a significant overstock.
Next Steps: For Item 1011:
- Analyze Sales: Examine historical sales trends to determine if low demand is driving excessive inventory.
- Review Procurement: Investigate ordering patterns for over-purchasing or discrepancies with demand forecasts.
Second-Level Analysis: Deeper Insights
Objective: Conduct a deep dive into item 1011 to uncover over-purchasing history by analyzing monthly sales trends compared to average inventory levels.
Prompt: For every month in 2022–2023, determine the sum of quantity sold compared to the average inventory for item 1011, including relevant details. Assume the date is September 1, 2023.
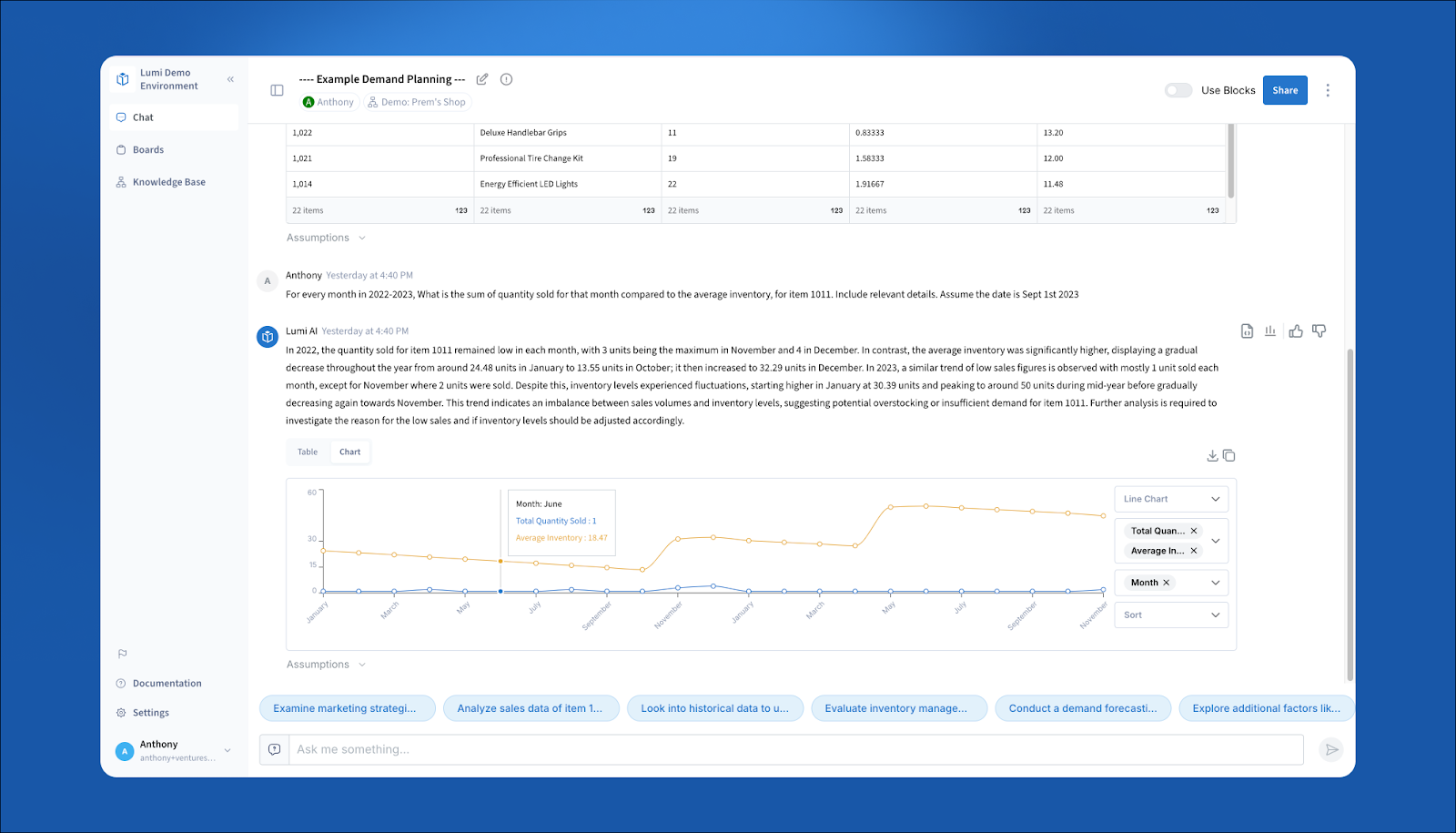
Outcome: The analysis revealed that item 1011 was re-purchased despite inventory levels significantly exceeding relative sales performance:
- 2022: Monthly sales remained low, peaking at 3–4 units, while average inventory levels ranged between 24–32 units.
- 2023: Similar trends were observed, with months like June recording a single unit sold compared to an average inventory of 38.47 units.
Next Step: Realign procurement mandates for item 1011 by:
- Reassess Stock Thresholds: Set statistically calculated min and max re-order points based on actual sales trends.
- Adjust Order Quantities: Modify procurement orders to better align with current demand patterns and reduce overstocking risks.
- Conduct Regular Reviews: Establish periodic reviews to ensure procurement aligns with changing demand dynamics and sales performance.
Key Insights and Recommendations
Adopt Real-Time Decision-Making Tools: Real-time dashboards and AI-driven analytics enable organizations to adapt to market changes swiftly, mitigating risks from customer behavior shifts and supplier instability.
Foster Democratized Collaboration: By enabling data access to more stakeholders from sales, marketing, and operations, organizations can enhance their forecasts' robustness.
Discover how Lumi AI can streamline your demand planning processes with advanced AI-driven insights and automation. Book your demo today.